Hermetic glass-to-metal seals, connectors, headers, and assemblies
Glass to metal connectors, headers, and seals can play a highly leveraged role in overall system performance. Glass to metal seal manufacturers may have different skill sets, so it’s important to choose an experienced manufacturer who can provide you with the high-quality hermetic seals your system needs.
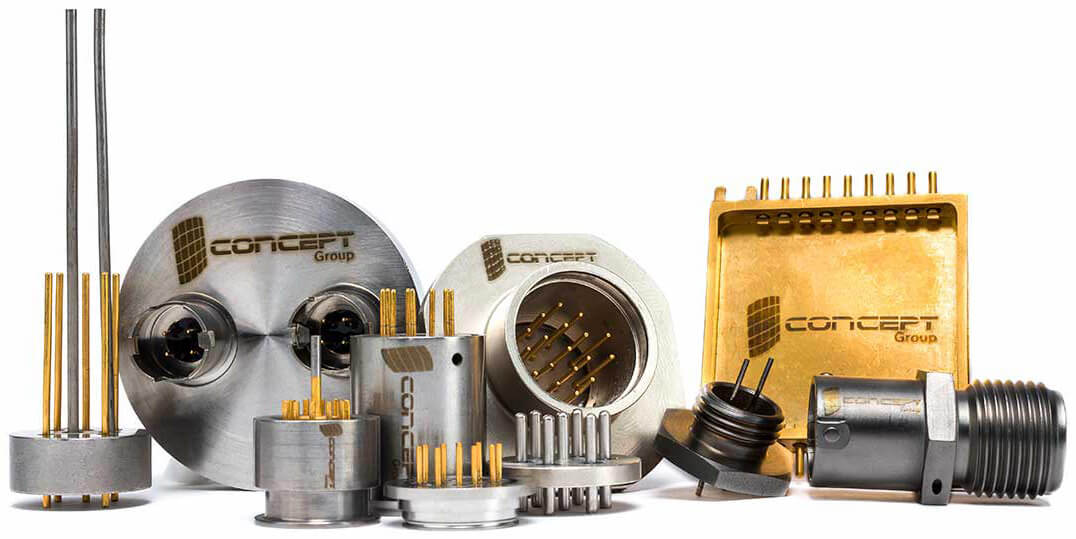
With over 50 years of experience and the most rigorous quality standards, you can count on Concept Group to deliver the high-quality hermetic connectors, headers, and seals your system requires.
High-temperature and high-pressure applications
We manufacture glass-to-metal compression seals for harsh environments including high-pressure and high-temperature applications.
Oxide-free final product
Our hermetic sealing process takes the job from start to finish including design support, machining, and joining. We deliver an oxide-free final product. Without an oxide layer, our seals are immediately weldable and ready to be integrated into your assembly out-of-the-box.
Compression sealing
We specialize in unmatched seals, also known as compression seals. Compression seals use materials with unmatched coefficients of thermal expansion (CTE) to ensure a hermetic bond between the glass and the metal. Our fully hermetic seals are suitable for high-temperature and high-pressure environments.
Material selection
Selecting the appropriate materials is of vital importance. We manufacture seals with stainless steel and titanium.
Frequently Asked Questions
What makes our glass to metal compression seals different?
There are many types of hermetic seals, and differences can have a dramatic effect on performance. Our glass to metal seal connectors and feedthroughs are made with stainless steel or titanium. With unmatched compression, our products are suitable for a wide range of challenging environments including high pressure and high temperatures.
What does it mean for seals to be weld-ready?
If your company does secondary welding, joining the seals to packages and other assemblies, you should use untarnished, weld-ready seals.
The manufacturing process used by many hermetic seal suppliers can leave a tarnish residue on metal parts. This thin tarnish layer melts at higher temperatures than welding metal, so it isn’t eliminated during your secondary welding. When you weld the tarnished seal into your packages and other sub-assemblies, the tarnish can get trapped in the new weld, producing a weld defect that’s very difficult to detect, even with radiography. This defect weakens the weld and can cause cracking and subsequent performance failure.
When is it important to use special, dense glasses?
If your application deals with high temperatures or high pressures, it’s important to select seals that are made with especially dense, strong glass. These denser glasses resist the cracking and other performance breakdowns that can occur when less dense glasses are subjected to such extreme conditions.
Your hermetic seals should also be manufactured under conditions of increased positive pressure. This positive pressure manufacturing process creates glasses of even greater density and reliability, by eliminating bubbles and voids that would likely remain if the manufacturing were done at lower or ambient pressures.
Do we clean incoming hermetic seals?
Many companies have to clean their incoming seals before they forward them to manufacturing. Tarnish on the seals’ metal surfaces can cause defects in your secondary welds, and these defects can produce weld cracking and other performance failures. That’s why the tarnish should be removed before you begin welding.
However, cleaning takes up valuable time, and that’s an added cost for your company. To eliminate this added cost, use weld-ready, tarnish-free seals that don’t need additional cleaning. In fact, in most applications, our seals can be used right out of the shipping container.
What if my glass to metal seals require plating?
Because most plating shops plate everything from doorknobs to car bumpers, they can be a significant source of cross-contamination. Impurities from such contamination can result in your hermetic seals blistering and turning brittle. The plating process can even deposit particulate contaminants, leading to rust.
If you need plating, it’s best to use an operation that specializes in plating glass to metal seals, one that works on nothing else. That way, you can be certain not only that the risk of cross-contamination is eliminated, but also that your precision-made seals are handled with appropriately rigorous quality control standards.